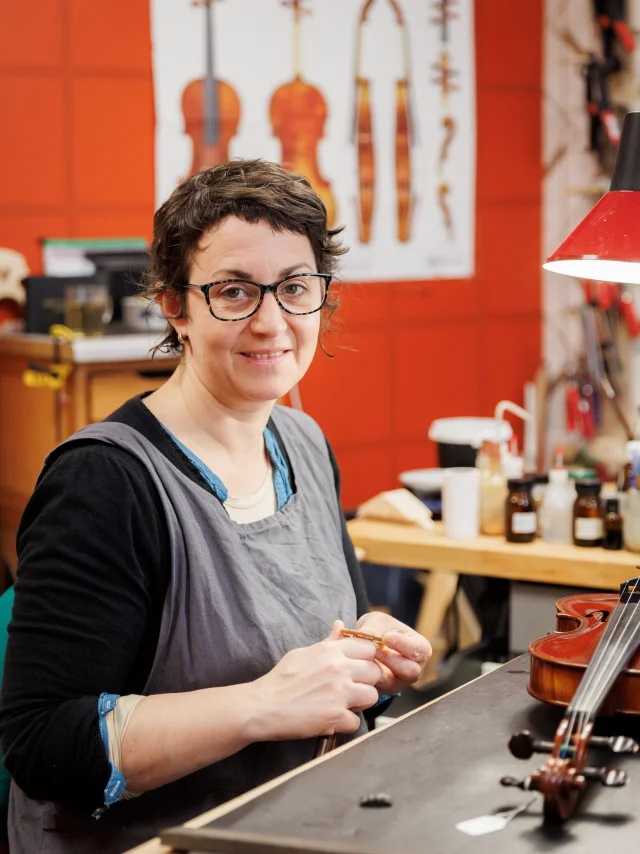
Can you describe your career path?
I was attracted to music from an early age, and becoming a luthier enabled me to become a link in the musical chain. Following university studies in musicology, I learned my trade at the International School of Violin Making in Newark-on-Trent, England, then continued my studies by taking part in high-level restoration courses in France, while working in various workshops in France, England and Italy.
What does your job involve?
Quartet lutherie encompasses a whole range of skills dedicated to the manufacture, restoration and maintenance of instruments in the bowed string family. From the majestic cello to the elegant violin, from the characterful viola to the imposing double bass, the luthier puts his heart and soul into each of these emblematic instruments. At the heart of this ancestral art, the luthier exercises his talent with meticulous care and expertise. Each instrument, whether an original creation or a meticulous restoration, requires a deep understanding of the material, construction techniques and unique sound characteristics of each piece. From the meticulous selection of precious woods to the delicate shaping of curves, every step of the process is a testament to the luthier’s dedication and exceptional craftsmanship. But lutherie is not limited to manufacturing. Restoring and maintaining old or damaged instruments is an important part of the luthier’s work. With patience and skill, the luthier brings tired instruments back to life, preserving their history and musical heritage for future generations.
What techniques do you use?
As the trade is a technical specialty, most techniques are specific to lutherie. One of the first crucial steps is the selection of the wood for the instrument. I choose top-quality woods, such as spruce for the soundboard and maple for the back, sides and neck. Then I carve using traditional tools such as gouges, planes and planes to cut and shape the various parts of the instrument. Once the parts have been cut and shaped, they are carefully assembled. This often involves the use of special glues and traditional assembly techniques to ensure the instrument’s strength and stability. Varnishing is an important step, involving the application of layers of varnish to the instrument. The varnish protects the wood and enhances its sound. Once the instrument has been assembled and varnished, I carry out careful adjustments to optimize its sound and playability.